Репортаж с производства Bassocontinuo: на чем стоит Италия
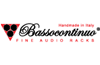
Итальянская аудиофильская техника — это всегда дорого, красиво, звучно и сделано вручную. Такая уж страна и таковы особенности бизнеса. Мне удалось увидеть итальянское мастерство и предпринимательский дух на производстве аудиофильских стоек Bassocontinuo. Кстати, дорогих, красивых, технически грамотных и сделанных практически полностью вручную.
Любая компания — это прежде всего люди. Самая важная персона в Bassocontinuo — ее основатель Лоренцо Беллоли (Lorenzo Belloli). Интеллигентный, вежливый итальянец с деловой хваткой и грамотной речью, кстати, вегетарианец, т.е. человек, придерживающийся определенного мировоззрения и принципов. В общем, типичный бизнесмен-пассионарий, увлеченный своим делом, и, что особенно интересно, новатор. Казалось бы, он делает стойки под аппаратуру, а что там можно придумать, кроме бесконечных заверений, что уж у нас-то виброразвязка точно лучше, чем у других. Оказывается, много чего еще можно придумать.
Лоренцо Беллоли, основатель и генеральный директор Bassocontinuo
Перво-наперво, несколько лет назад, Беллоли придумал делать стойки под определенную технику. Примерно в двух часах езды от итальянского города Бергамо, где базируется Bassocontinuo, расположен город Виченца, где была основана и до сих пор живет компания Sonus Faber. Если вы следили за перипетиями аудиокорпораций, то знаете, что в 2012 году Fine Sounds (итальянский холдинг, куда входила Sonus Faber) приобрел американскую фирму McIntosh Laboratory. А с 2016 года вся эта корпорация из пяти брендов стала называться McIntosh Group.
О работе этого холдинга я расскажу в другом репортаже — мне повезло побывать и в Виченце, а сейчас вернусь к Лоренцо Беллоли. Географическая близость и знакомства по аудиовыставкам и навели итальянского конструктора на мысль попробовать сделать стойку специально под технику McIntosh. Компоненты этого бренда имеют легко узнаваемый дизайн — зеленый логотип, стрелки индикации уровня с синей подсветкой, каемку регуляторов и боковые «уши». Потому и можно создать мебель под стать аппаратам, достичь стилистической общности. Конечно, добавив к этому техническое обоснование — правильную виброразвязку.
Тут следует сказать, что Беллоли делал стойки и до появления этой идеи (Bassocontinuo основана в 2008 году), поэтому сначала он конкурировал исключительно качеством виброизоляции. Отсюда — карбоновые опоры для полок (у самых полок нет параллельных граней) и специальная форма металлического конуса для понижения частоты резонанса. Вставки — из оригинального абсорбера Technogel (этот материал одноименной американской компании применяется в медицине, производстве обуви и т.п., по свойствам близок к силиконовому гелю), шарик из торлона для виброразвязки в стойках под винил. Иными словами, инженерная часть его творений хорошо продумана и напрочь лишена эзотерики.
Стойки из линейки «B by Bassocontinuo» специально под компоненты McIntosh
И, как говорит нам принцип Анны Карениной, чтобы прийти к успеху, нужно, чтобы совпало огромное количество факторов, и случай линейки «B by Bassocontinuo» эту теорию хорошо подтверждает. Судите сами: поблизости оказывается менеджмент McIntosh — совсем не дешевый бренд, для продукции которого можно делать дорогие и качественные аксессуары. Тогда как сама Bassocontinuo — маленькая итальянская компания со штучным ручным производством, и тут о масспродакте и речи быть не может.
В городе Бергамо находится огромное количество различных небольших фабрик: металл, обработка кожи, швейные мастерские, покрасочные, деревообработка и т.д., то есть можно реализовать фактически любые технические решения. Наконец, сам Лоренцо Беллоли, сумевший не только разработать мебель, но и организовать производство деталей на нескольких итальянских фабриках, объединить «потоки» и выпустить конечный продукт.
Собственно, презентационный тур, который устроил Беллоли и российский дистрибьютор Armada Sound для журналистов и дилеров, состоял из посещения этих мини-предприятий в Бергамо. Когда мы ехали на очередной заводик на соседней улице, я, честно скажу, больше всего удивлялся, насколько практично все получилось в этом маленьком городке Северной Италии. Огромный кластер компаний позволяет выпускать очень разную продукцию, ведь легко найти производителя чего угодно на расстоянии в несколько километров.
Понятно, что в силу небольших размеров этих производств, работа на них ведется вручную, а значит, стоит дорого. С другой стороны, слова «Handmade in Italy» для многих людей служат маркером качественной вещи. Я, кстати, раньше относился к ним с большим недоверием, а здесь наглядно увидел, что действительно все делают вручную, автоматизированный труд применяется только там, где руками это сделать невозможно или займет слишком много времени. Ну что ж, поехали.
Вначале было дерево
Первой остановкой на нашем пути стала фабрика обработки деревянных деталей. К сожалению, ее мы посетили вечером, поэтому работы на ней уже не велись, и как именно там «пилят-строгают» увидеть не удалось. Беллоли рассказал, что на этом предприятии для Bassocontinuo в год делается около 3,5 тыс. полок. Здесь же наносят отделку разными видами шпона — проклеивают, потому выдерживают не менее получаса под 5-тонным прессом.
Я не уверен, что конкретно эти древесные плиты пойдут на изготовление
полок Bassocntinuo, но именно с этого все начинается
А это уже выпиленные полки, некоторые с отделкой
После того как полки выпилены и отшлифованы, они уходят на другие фабрики, но некоторые из
них возвращаются, чтобы здесь закрепили стекло на их верхнюю сторону
Так полка выглядит после приклеивания стекла
Прототип полки с нижней светодиодной подсветкой впервые показали на Munich High End в прошлом году.
Беллоли рассказал, что включение-выключение подсветки сделают сенсорным — пользователю нужно лишь
махнуть рукой около полки. Также опционально выпустят пульт ДУ с возможностью
регулировки оттенка цвета, будет доступно и триггерное управление
Ровные неровные швы
Потом мы посетили фабрику по работе с кожей. Некоторые полки в каталоге Bassocontinuo отделаны кожей или алькантарой (совсем не дешевая микрофибра, которая применяется в отделке дорогих автомобилей). Беллоли заверил, что они берут только натуральную качественную кожу, и на выбор покупателю предлагается более 200 вариантов.
Процесс обработки включает несколько шагов. Сначала отбираются куски без царапин или вмятин. Затем по картонному лекалу вырезаются части, из которых потом сошьют «чехол». Собственно, главная специализация этого производства — пошив. В случае с отделкой полок швы должны быть красивыми, крепкими и ровными. Однако абсолютной машинной ровности не требуется, ведь работы ведутся вручную и небольшие отклонения, наоборот, придадут продукту «крафтовости». Зато гарантируется высокое качество — на этой же фабрике шьют кожаные изделия для премиальных брендов (при нас там доделывали партию женских сумок с ценником в 3,5 тысячи евро, но попросили не фотографировать этот процесс и не называть бренд).
Так выглядит готовый чехол для полки
Кожу очищают с обратной стороны загиба, готовят к проклейке
Шов буквально «отбивают», чтобы не было утолщения и он получился ровным.
Посмотрите, как это работает на видео в конце статьи
На получившемся изделии обязательно выдавливают штамп Vera Pelle. Это не название
бренда, а просто слова «натуральная кожа» на итальянском языке
Прошивку делают вручную на швейной машинке
Нержавеющая сталь
Этой небольшой фабрикой по обработке металла владеют (и работают на ней) два брата Мауро и Карло Локателли (Mauro и Carlo Locatelli). Один занимается фрезерными станками с ЧПУ, а другой — ручной финишной отделкой. Изначально на фабрику поступают длинные 6-метровые цилиндрические стальные стержни. Для продукции Bassocontinuo они применяют только коррозионно-стойкие стали. Это потому, объяснил Беллоли, что стойки поставляются по всему миру, а в теплых азиатских странах, например, металл быстро ржавеет из-за повышенной влажности.
Братья Локателли рассказывают о своем производстве
Стальные стержни, из которых делают все металлические детали стоек
Стержень нарезается на отрезки
Далее эти нарезки поступают во фрезерный станок с программным управлением
Готовые изделия: ножки, конусы, втулки
Это будет подставка для оригинальной версии стоек Accordeon с тремя белыми лакированными полками.
Ножки при помощи анодирования делают вот такого благородного серого цвета
Покрасить и отполировать
Следующая фабрика встретила нас резкими запахами. Можно сказать, что это было одно из самых неэкологичных мест, но никуда от этой процедуры не деться — покраска. Помимо деревянных полок для Bassocontinuo, также красят стекло.
Собственно, со стеклом все просто: сначала его тщательно отмывают с применением обезжиривающего моющего средства, после чего покрывают водной краской. Нужен всего один слой (и, как вы понимаете, с одной стороны) — и стекло готово. Вся процедура, включая просушку, занимает один день.
Покраска деревянных полок уже не так проста. Сначала поверхность шлифуют, а затем наносят трехслойное покрытие светлой грунтовкой. После высыхания (около двух дней) и шлифовки уже покрывают краской (под дерево) или лаком. В первом случае нужно три слоя, чтобы достичь результата, а вот для лакировки — уже шесть (дважды по три слоя). Между каждым покрытием и высыханием идет тщательная проверка на дефекты, которые при необходимости грунтуются и шлифуются. Проблема еще и в том, что нельзя покрасить сразу две стороны полки, поэтому вся процедура получается долгой — около трех недель.
После этого одну сторону стекла покрывают водной краской
Так выглядит панель после грунтовки
А так после первого слоя лакировки
Перед полировкой на машине рабочий смазал поверхность полировальной пастой
На машине (фото выше) получается отполировать только верх
и низ полки, а боковые поверхности обрабатываются вручную
На складе
Дальше мы оказались на складе Bassocontinuo, где происходит не только хранение коробок, но, собственно, и упаковка всех этих деталей в коробки. Думаю, читатели понимают, что стойки поставляются в разобранном виде, собирают их уже у покупателя дома. Поэтому фактически после изготовления всех частей нужно просто их аккуратно упаковать и отправить в магазины. Я не буду здесь рассказывать о хитростях упаковки, упомяну лишь, что Лоренцо Беллоли продумал все досконально, и, конечно, упаковка тестировалась на падения и тряску, так что покупатель получит полки в полной сохранности.
Специально для нашей группы на склад приехал подрядчик, мастер по кожаной отделке Андреа Инноченти (Andrea Innocenti), который наклеивает кожу на полки. Как он объяснил, его мастерская слишком маленькая, чтобы там поместились еще и пара десятков зрителей, поэтому процесс наклейки он покажет прямо здесь. От слов к делу — все заготовки были уже на месте.
Никаких секретов в этой процедуре нет, однако она требует аккуратности и, как подчеркнул Беллоли, у Андреа нет права на ошибку. Если что-то пойдет не так, не получится это исправить, придется выкидывать всю полку. Мастер покрывает клеем дерево, после накладывает кожу, выравнивает покрытие. На одну полку уходит около полутора часов. Процесс частично запечатлен на видео в конце статьи.
Лоренцо Беллоли показывает, как правильно складываются кусочки пенопластового «пазла» в коробке
Так выглядят «исходники» прежде чем за них возьмется Андреа
Далее Андреа натягивает кожу на полку
Чтобы закрепить кожу, помимо клея используются заклепки
Металлические вставки остаются в пазах, пока не высохнет клей
Для сокрытия «швов» используется вот такой кожаный шнур
По окончании работ на полке закрепляют набор ярлычков, среди которых сертификация о том, что все сделано вручную в
Италии, а также серийный номер изделия. Стоит отметить, что компания хранит в базе
данных всю информацию о каждом продукте по его серийному номеру — от подробностей производства до места поставки
Этот шарик — специальный виброизолятор, сделанный из торлона — пластика с особыми свойствами (в шесть раз жестче стали,
но при этом эластичного). Его часто применяют в аэрокосмической индустрии.
И в продукции Bassocontinuo — для виброразвязки полок для винила
Поглощение резонансов
Следующая фабрика на нашем пути занималась производством карбоновых деталей. К сожалению, на ней нам запретили фотографировать (там делают некоторые детали корпусов воздушных фильтров и интеркулеров для Ferrari), поэтому я лишь кратко расскажу о ней и приведу пару фотографий, позже присланных мне организаторами поездки.
Оказывается, изначально карбоновое полотно (да, именно так — плетеная ткань) приходит в рулонах и хранится в холодильнике. Обычно толщина этой ткани небольшая — меньше миллиметра. Ее нарезают по выкройке, складывают в несколько слоев — их может быть 5, а может и 50, зависит от того, насколько крепкий и толстый продукт нужно получить на выходе. После этого складывают в гипсовую или алюминиевую форму (матрицу), заливают смолой и запекают в печи. Звучит просто, но на практике это высокотехнологичный процесс и ручного труда в нем немного — только укладка и последующая шлифовка.
Работник фабрики склеивает слои карбонового волокна в матрице для запекания
Так выглядит вблизи алюминиевая матрица, где запекают карбон
Другой вопрос, зачем вообще карбон в полках под аппаратуру? Как объяснил Лоренцо Беллоли, конус снижает частоту резонанса (вибрации), тем самым уводит его в неслышимую область, уменьшает влияние на электронику. Но тем не менее не избавляет от резонансов вообще. В линейке Revolution Беллоли попытался кардинально решить проблему — поглотить резонанс полностью.
На этих фото хорошо видно, что полка соприкасается с крестовиной через круглые прокладки из абсорбера
Для этих целей полка ставится на карбоновую крестовину (причем сама полка может быть выполнена из дерева, карбона или иметь карбоновую вставку, но это уже не имеет для виброразвязки никакого значения, декоративная функция). Эта крестовина весит около 300 грамм и выдерживает (не деформируется) массу до 130 кг, а чтобы ее сломать, нужно применить усилие примерно в полтонны.
Но и это не все. В местах соприкосновения крестовины и полки расположены прокладки из абсорбера Technogel, по свойствам похожему на силикон. Таким образом, получается, что опора — легкая, сочленения — аналог мягкой резины. Под виниловые проигрыватели Лоренцо рекомендует полки именно такой конструкции.
На этом наше путешествие подходит к концу, а некоторые моменты производства вживую смотрите на видео:
Источник: stereo.ru